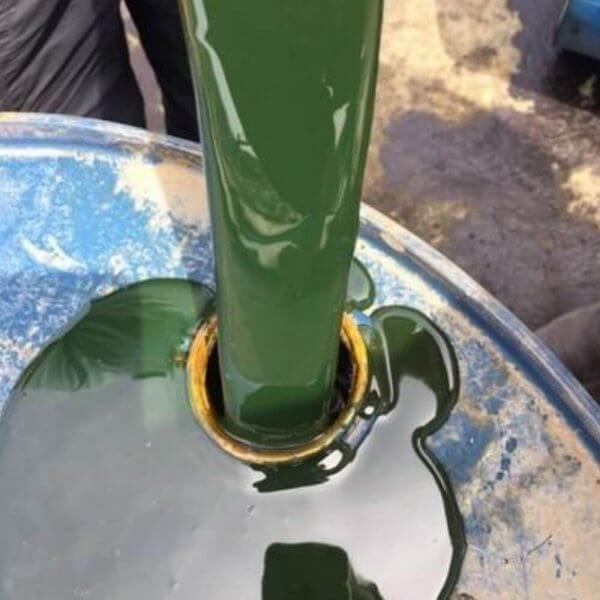
Quick Brief to RPO Types

Abstract:
Rubber process oil (RPO) plays a pivotal role in the rubber industry by enhancing the processing and performance of rubber compounds. This comprehensive article delves into the characteristics, types, and various applications of RPO. From tire manufacturing to industrial rubber goods, the article explores how RPO contributes to improving the quality and efficiency of rubber processing, ensuring the fdvfv dfdf dfdfcreation of durable and high-performing rubber products.
Introduction:
Rubber process oil is a vital component in rubber processing that enables manufacturers to achieve the desired properties of rubber products. It is a type of specialized petroleum-derived product used as a processing aid, softening agent, and extender for rubber compounds. RPO is designed to enhance the plasticity and workability of rubber, leading to superior finished products across a wide range of industries.